China Silicone Supply Excellent Adhesion Silicone Resin Substitute for Shin-Etsu KR-220L.
General Features:Appearance: White solid
Volatilization 105℃3h (%): 1.0
OH content (wt%) :4.0
Softening point(℃): 70
Curing time (s): 200
ApplicationsChinese factory supplies silicone resin with excellent adhesion to inorganic materials Similar to Shin-Etsu KR-220L.
1.Powder coatings
2.Coatings for resistors3.Adhesive for electrical and electronic parts
4.Adhesive for mica lamination (supports for nickel-plated alloy wires in irons, hair dryers, ovens, etc., heat-resistant washers, insulation for high-temperature equipment, insulation boards, partition boards for microwave ovens, etc.)5.Coloring agent for flame-retardant coatings
UsageReplacement product for Shin-Etsu KR-220L Silicone Resin.
<Mica laminated sheet>
1) Please confirm the appropriate curing time before use.
2) Since the purpose of the drying process is to remove the solvent, if the conditions are too strong, sometimes sufficient adhesion cannot be obtained. Mix the following proportions and spread 8% to 10% of silicone on the integrated mica using a sprayer.
Forming under the following conditions
Compounding | SilibaseSRD-220L 60 parts Toluene 440 parts Propanol 100 parts D-234 1.2 parts |
Drying (vulcanization) | 100~105 ℃/5min |
Vulcanization | 180 ℃/60min*9.8MPa |
Maturation | 100 ℃/12h→150 ℃/4h→ 200 ℃/2h→250 ℃/2h→320 ℃/2h |
1: Acid catalyst, colorless transparent liquid
Appearance | | Smooth surface |
Bending strength N/mm2 | Normal | 177 |
| 50℃/24h/100%RH | 137 |
Insulation breakdown strength kV | Normal*2 | 23.0 |
| 23℃ water 24h immersion*2 | 20.4 |
Volume resistivity Ω.m | Normal | 4.2*1014 |
| 23℃ water 24h immersion | 5.2*1012 |
2: Thickness 0.42mm
Molding compound (binder for inorganic filler)
5-30% of the total compound can be mixed as follows.
1) Dry blend
Chinese Factory of Analogue heat resistance silicone resin Shin-Etsu KR-220L.
Grind SilibaseSRD-220L with a 100 mesh sieve, mix it with inorganic fillers at room temperature, and add 0.1 to 0.5 wt% of hardening catalyst to SilibaseSRD-220L as necessary to obtain a compound with good storage stability.
2) Solution mixture
Mix SilibaseSRD-220L with inorganic fillers in an appropriate solvent, dissolve SilibaseSRD-220L in 30-50% concentration of toluene, methyl-ethyl ketone, etc., add 0.1-0.5wt% hardening catalyst (aluminum, titanium, zinc) to SilibaseSRD-220L as necessary, add inorganic fillers and mix thoroughly, then remove the solvent by vacuum drying, spray drying, etc. to obtain the compound.
3) Molten compound
SilibaseSRD-220L is melted and flowed at 70-150℃, and mixed with inorganic fillers using a hot mill or the like. If necessary, add 0.25wt% or less of a hardening catalyst to SilibaseSRD-220L, and mix to obtain a mixture. The mixture made according to the above steps is solid or powdery, and can be pressed and formed at 150-180℃. The forming time varies depending on the presence, type, and amount of the catalyst, and 5-30min is required. If secondary hardening is performed at 200℃/2-6h, the properties will be improved. When ceramicizing, start from 200℃, gradually increase the temperature by 20-50℃, and sinter at 600-1000℃. In addition, a certain amount of smoke is acceptable at 300-500℃.
<Flame retardant paint>
By mixing in potassium chloride according to the following ratio, a flame retardant coating that is almost non-flammable can be produced.
Cooperate | SilibaseSRD-220L 15 parts Silicon dioxide powder 10 parts Red pigment 5 parts Clay 30 parts Alcohol 80 parts Toluene 20 parts |
<Powder coating>
SilibaseSRD-220L, 20-40 parts by weight, inorganic filler (such as alumina, silica, magnesium oxide, tarque, clay, etc.), 60-80 parts by weight, hardening catalyst (aluminum, titanium, zinc) is added as necessary, kneaded in a hot roller (100-130°C), and crushed. By fluidized dipping method and electrostatic coating method, a coating film with excellent flame retardancy can be obtained.
Reference Data
【Heating loss】
Take 0.2g of SilibaseSRD-220L, heat it from room temperature to 800℃ at a rate of 2℃ per minute, and measure the heating loss. (In nitrogen)
Heating reduction according to thermobalance
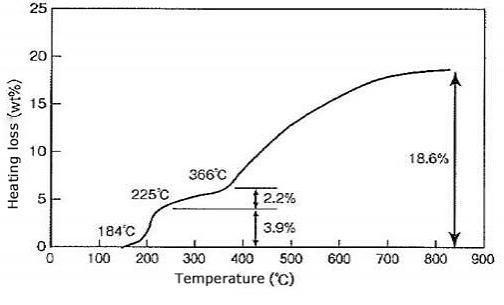
【Thermal expansion coefficient of hardened material】
Hardening conditions | Thermal expansion coefficient 20~150℃ |
150℃/40h | 2.3×10-4/℃ |
200℃/40h | 1.6×10-4/℃ |
250℃/40h | 1.3×10-4/℃ |
Notes on UseExcellent Flame Retardancy silicone resin is Substitute for Shin-Etsu KR-220L.
1) It must be sealed and stored in a cool and dark place (a place below 25℃ and not exposed to direct sunlight).
2) Please wear protective tools (rubber gloves, safety glasses, etc.) when using, and do not let it adhere to the skin or mucous membranes. If it adheres, please wash it off immediately with soapy water or running water. In addition, if you use it under dusty conditions, please wear a dust mask.
3) If it enters your eyes, immediately rinse it with clean running water for more than 15 minutes and consult a doctor.
4) When it is turbid when dissolved in a solvent, adding a small amount of alcohol such as propanol can make it uniform.
5) This product is not a dangerous substance under the Fire Protection Act.
6) Please read the product safety data sheet (MSDS) carefully before use. Please ask the sales department in charge for the MSDS. The mixing of acids, alkalis, and certain organic metal compounds may have a negative impact on storage stability. When mixing fillers, pigments, etc., conduct tests in advance and confirm the impact before use.
Packaging10kg (cardboard barrel)